Comprehensive Overview: What is Porosity in Welding and Just How to stop It
Comprehensive Overview: What is Porosity in Welding and Just How to stop It
Blog Article
Porosity in Welding: Identifying Common Issues and Implementing Finest Practices for Avoidance
Porosity in welding is a pervasive concern that commonly goes unnoticed until it creates considerable problems with the integrity of welds. In this conversation, we will explore the crucial elements contributing to porosity development, examine its detrimental results on weld efficiency, and talk about the best techniques that can be embraced to minimize porosity event in welding processes.
Usual Reasons For Porosity
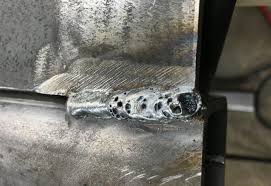
Using dirty or wet filler products can present contaminations into the weld, contributing to porosity problems. To alleviate these usual reasons of porosity, thorough cleaning of base metals, appropriate securing gas option, and adherence to optimum welding parameters are important methods in accomplishing high-grade, porosity-free welds.
Influence of Porosity on Weld Quality

The visibility of porosity in welding can dramatically endanger the architectural integrity and mechanical homes of welded joints. Porosity creates gaps within the weld steel, compromising its overall toughness and load-bearing ability.
Welds with high porosity degrees often tend to display reduced impact toughness and decreased capacity to deform plastically prior to fracturing. Porosity can impede the weld's capability to properly transfer pressures, leading to premature weld failing and prospective safety threats in essential structures.
Finest Practices for Porosity Avoidance
To enhance the structural integrity and top quality of bonded joints, what certain procedures can be carried out to lessen the incident of porosity during the welding process? Making use of the proper welding method for the certain material being welded, such as readjusting the welding angle and weapon setting, can even more prevent porosity. Normal examination of welds and instant remediation of any concerns determined during the welding procedure are necessary methods to avoid porosity and produce high-grade welds.
Value of Appropriate Welding Techniques
Applying correct welding techniques is vital in ensuring the structural honesty and quality of welded joints, developing upon the structure of effective porosity prevention actions. Excessive warm can lead to raised porosity due to the entrapment of gases in the weld pool. Furthermore, making use of the appropriate welding specifications, such as voltage, existing, and take a trip rate, is important for accomplishing sound welds with marginal porosity.
Moreover, the selection of welding process, whether it be MIG, TIG, or stick welding, ought to line up with the certain needs of the project to ensure ideal results. Proper Look At This cleaning and preparation of the base metal, as well as choosing the ideal filler product, are additionally essential components of skilled welding strategies. By sticking to these ideal methods, welders can lessen the threat of porosity development and generate high-grade, structurally sound welds.
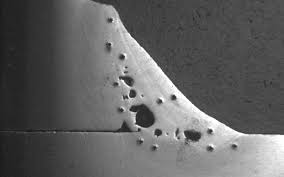
Testing and Top Quality Control Procedures
Testing procedures are important to spot and avoid porosity in welding, guaranteeing the strength and resilience of the final product. Non-destructive screening approaches such as ultrasonic screening, radiographic testing, and visual evaluation are commonly employed to recognize possible flaws like porosity.
Carrying out pre-weld and post-weld inspections is additionally important in preserving quality control criteria. Pre-weld assessments include verifying the products, devices setups, and tidiness of the job area to stop contamination. Post-weld examinations, on the other hand, examine the final weld for any type of defects, consisting of porosity, and validate that it fulfills defined standards. Applying an extensive top quality control plan that consists of extensive screening procedures and examinations is vital to reducing porosity problems and ensuring the general top quality of visit our website welded joints.
Verdict
To conclude, porosity in welding can be a typical concern that influences the quality of welds. By determining the usual sources of porosity and implementing best methods for avoidance, such as correct welding techniques and testing steps, welders can make sure top quality and reliable welds. It is important to useful content prioritize avoidance techniques to decrease the event of porosity and maintain the integrity of welded structures.
Report this page